As an important component of the vehicle suspension system, shock absorbers play a crucial role in reducing the vibrations transmitted by the vehicle body and frame. They mitigate the impacts and energy from uneven road conditions during driving. The application of shock absorbers significantly improves driving comfort and ensures the safety of passengers and cargo. Additionally, because shock absorbers work within the vehicle’s chassis suspension system, they must withstand exposure to dust, sewage, varying temperatures, impacts, and foreign objects from the roadside. Therefore, there are high requirements for the surface coating quality of shock absorbers. Considering the different structural designs of vehicles, the appearance of shock absorbers also varies greatly, especially those with trays. During the coating process, there are many blind spots that require additional pre-spraying or touch-up spraying to enhance both the quality and efficiency of shock absorber production.
In traditional spray painting processes, whether using an overhead conveyor or a ground track system, operators usually manually pre-spray complex structural parts of the shock absorber to avoid any unpainted spots. After ensuring that each critical area is adequately covered, the product is then automatically moved into the range of a rotary atomizer for overall surface coating. During this process, it is essential to ensure that the manual work efficiency matches the rhythm of the production line. However, in practice, even if operators are working long hours at high intensity on pre-spraying tasks, they often cannot match the processing efficiency of the rear-end electrostatic rotary atomizer, leading to limitations in overall production capacity. Additionally, frequent repetitive manual operations can cause extreme fatigue among workers, resulting in a decline in spray quality and instances of coating defects
SUNSEK’s automated robotic painting solution for shock absorbers combines advanced electrostatic spinning disc technology and six-axis robots to achieve efficient and precise painting operations. This solution not only enhances the painting quality and efficiency of complex shock absorbers but also avoids the adverse health effects associated with manual operations, reducing management costs and safety risks for enterprises. The entire process requires no human intervention, automating both pre-painting and full-painting processes to ensure even coverage in every corner, significantly improving production efficiency and paint yield. Additionally, this solution offers high flexibility, capable of accommodating the painting needs of different models and sizes of shock absorbers, providing enterprises with a one-stop intelligent painting solution. In practical applications, the SUNSEK system can automatically recognize the shape and size of the workpiece, adjusting the painting path and angle to ensure perfect handling of every detail. Moreover, the system employs intelligent control software that can monitor and adjust painting parameters in real time, ensuring uniformity and consistency of the coating.
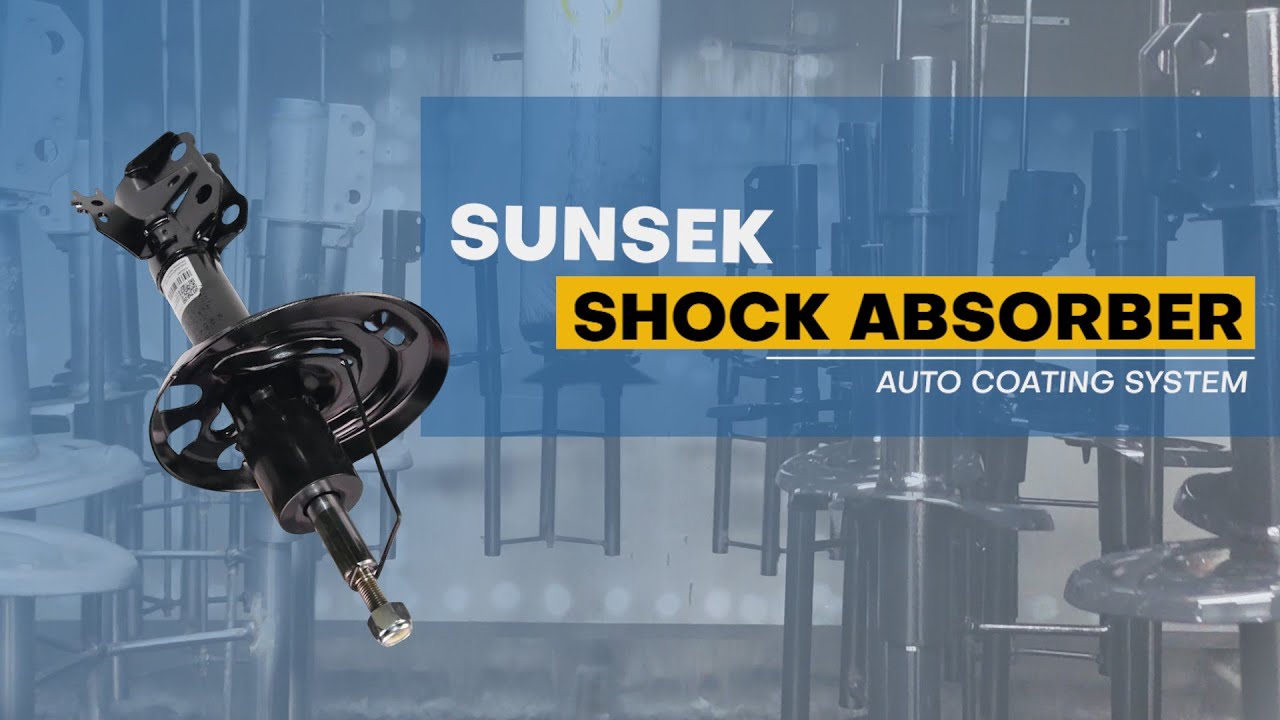